Mon 23rd May 2022 - What is Considered a Low Voltage Motor?
This is a tricky one to answer – the Low Voltage Directive defines low voltage from 50 – 1000 Vac, or 120 – 1500 Vdc, which is based on the mains voltage used to power the electrical system and ties in with specific IEC regulations on safety and risk of shock and arcing. When low voltage motors are discussed in the context of servo motors however, low voltage is focused on battery operated applications. While standard industry brushless motors are typically operated at 120 – 480 Vac, low voltage servo motors are optimized at voltages ranging for 24 – 96 Vdc. By definition, voltages in this range are considered by the IEC to be in the Extra Low Voltage (ELV) category.
What makes a motor low voltage?
A servo motor is powered by a drive that obtains power from either an AC or DC source. Two specific motor parameters determine the motor’s speed/torque characteristics – the back EMF (Kb) measured in Volts/krpm, and torque sensitivity (Kt)measured by Nm/A. The motor speed is directly related to the applied voltage, and the motor torque is directly rated to the applied current. These two characteristics are directly affected by how many turns of wire are used in the motor coils, with the motor winding typically optimized for the voltage intended for the application. A motor can operate at voltages up to its maximum voltage rating, which is based on the insulation system used in the motor construction.
Example: A motor rated at 2000 rpm with a rated torque of 5 Nm will utilize windings with 10 turns per coil having a voltage rating of 170 Vdc and current rating of 10 A. If this motor was powered with 85Vdc and no adjustments were made to the winding, it would only be capable of 1000 rpm at 5 Nm (assuming the same current is available at the lower voltage). To operate at the same power level with a lower voltage, the motor winding would be adjusted by reducing the number of turns (5 turns per coil) to achieve 2000 rpm at 85 Vdc. However, doing this changes the motor torque sensitivity characteristics and, to achieve 5 Nm of torque at 2000 rpm with 85 Vdc, 20 amps will now be required.
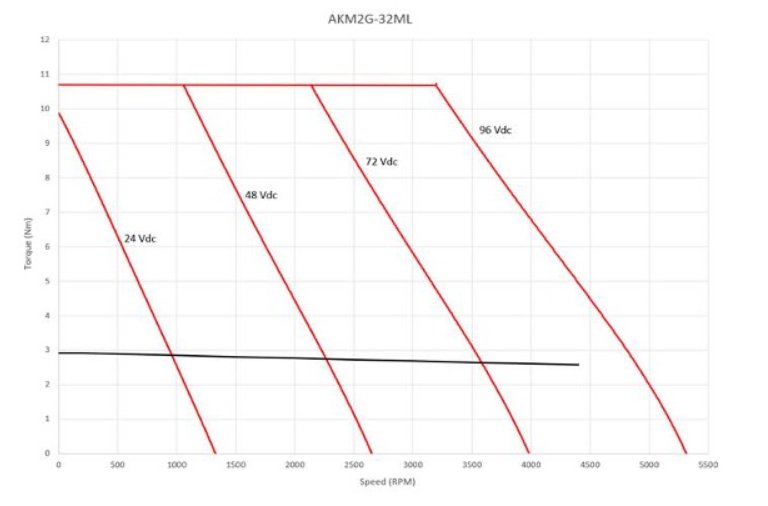
Consider typical battery-operated applications, such as remotely operated vehicles (ROV’s) or Robotics, where voltage from 24 – 96 Vdc are utilized. The servo motor would need to contain windings that were optimized to meet the load point at the specific applied voltage and available current. These applications are ideal for low voltage motor solutions since the application requirements are typically lower speeds and higher torque. However, a low voltage motor may be applicable for operation at higher speeds as well if the motor windings are optimized for efficient operation at the rated speed, torque, available voltage and current.
About the Author
This blog was a collaborative effort among a team of motion and automation experts at Kollmorgen, including engineers, customer service and design experts.
=======================================================================================================================================================================
As a Gold Partner, Micromech are able to supply and provide expertise on
Kollmorgen products. Contact our sales team on
01376 333333 or
sales@micromech.co.uk for price and delivery or technical assistance.
Disclaimer
The use of this news article and images came with permission from Kollmorgen.