Mon 3rd Oct 2022 - The Big Debate – Stepper vs Servo
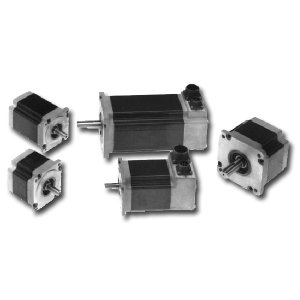
What is the best motor technology to use in a motion control application? There are numerous technologies to create motion, from hydraulic to pneumatic or electromechanical. In the world of precision motion control, many machine designers face a choice between step motor or servo motor technologies to solve their performance requirements. Both stepper motors and servo motors have a place in the motion control world but understanding when to use each has created a big debate.
Let’s check in on the ongoing debate of stepper vs servo…
Engineer A: "I like using stepper motors. They are simple to use, easy to set up and are reliable. I don’t need a lot of fancy control schemes to get my system from point A to point B.”
Engineer B: "I prefer a servo motor. The ability to cover a wide speed and torque range suits my multi-axis machine design perfectly.”
The engineers in this debate come from two different industries and have vastly different mechanical systems. Engineer A likes the simplicity of the stepper motor – from its set up and operation to how easy it is to get up and running. Based on the comment about point-to-point positioning, Engineer A has likely chosen the best solution for their particular machine. Stepper motors are a solid choice for simple point to point applications where load disturbances are minimal. Engineer B prefers the broad capabilities of servo motors, which makes sense in applications that require precise control and have multiple axes of coordinated motion. The high bandwidth and precision control of closed loop servo motors makes tight coordinated motion possible for multi-axis machinery.
Engineer B: "I had a bad experience with stepper motors when we attempted to use them on an axis with varying load disturbances.”
Engineer A: "I tried using a servo, but when it reached position it moved back and forth slightly as it came to a stop, which caused issues in the product finish.”
When Engineer B used a stepper motor on an axis that had some unpredictable load disturbances, some of these variations caused the motor to lose count, which eventually caused position errors. While this issue can be corrected by adding feedback to the stepper motor, it highlights one application where the open loop stepper may not be the best choice. In Engineer A’s case, an improperly tuned servo motor may "hunt” for position. Move and settle times can vary from application to application depending on motor sizing, inertia mismatch, and servo loop tuning. In the case of a simple point to point move with minimal load disturbances, a stepper motor is likely a better choice to stop at the designated point and hold position without hunting.
For Engineer A, the simple point to point positioning was best served using a stepper motor, while for Engineer B, the multi-axis coordination was better accommodated with servo motors. This "debate” explores only a few attributes that can influence the choice of servo vs stepper. To help determine which motor technology best fits each situation, Kollmorgen reviews numerous application attributes in the white paper
"Stepper Motor vs Servo Motor – Which Should it Be?”
This blog was a collaborative effort among a team of motion and automation experts at Kollmorgen, including engineers, customer service and design experts.
====================================================================================================================================================================
As a Gold Partner, Micromech are able to supply and provide expertise on
Kollmorgen products. Contact our sales team on
01376 333333 or
sales@micromech.co.uk for price and delivery or technical assistance.
Disclaimer
The use of this news article and images came with permission from Kollmorgen.