Mon 29th Mar 2021 - How Does a Servo Drive Work? Kollmorgen Experts Explain
A servo drive is an electronic device that is part of a closed loop system, producing current and voltage to rotate a servo motor. The closed loop system includes the servo drive, servo motor and feedback device, and is commanded from an analog or digital signal.
Servo drives are available in various voltage and current ratings and may provide position, velocity, and/or torque control. A wide range of servo motor types are controlled using servo drives, including AC, DC , brushed, brushless, rotary, or linear motors. The feedback device can be a potentiometer, Hall effects, tachometer, resolver, encoder, linear transducer, or any other sensor as appropriate. The servo drive powers the motor and compares the feedback data and command reference to verify that the servo motor is operating as commanded. The command signal is supplied from a variety of sources, most commonly from a PLC, CNC, or motion controller.
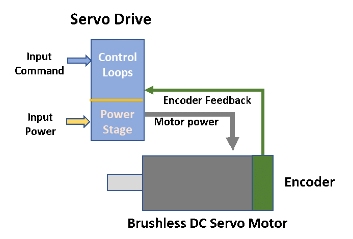
Breaking down a servo drive further reveals two major elements common in all servo drives – the power stage and servo loops. The drive power stage begins with input power from an AC or DC source and utilizes transistors in an H bridge configuration to deliver power to the servo motor. The transistors act as switches to facilitate voltage and current flow though the servo motor in either direction, providing forward or reverse motion.
The servo loops provide proportional control of the motor based on an input command signal. A simple servo drive may contain a single servo loop to control torque. More advanced servo drives add a velocity loop and may also contain a position loop. In a complete servo drive system, a digital signal provided by a motion controller will command a desired motion profile utilizing all three servo loops tuned for optimum performance. Each loop signals the subsequent loop and monitors the appropriate feedback elements to make real time corrections to match the commanded parameters.
Servo drives are available as ASIC chips where an electronic design engineer may integrate into a customized control platform, or as ready to connect "box” built units. In addition, servo drives are available integrated into motion controllers with ample I/O and safety elements in a single package.
Know your current and voltage requirements for a drive? Enter your specifications to search and compare our products, identifying what best fits your needs with our Product Selectors tool.
About the Author
This blog was a collaborative effort among a team of motion and automation experts at Kollmorgen, including engineers, customer service and design experts.
As a Gold Partner, Micromech are able to supply and provide expertise on
Kollmorgen products. Contact our sales team on
01376 333333 or
sales@micromech.co.uk for price and delivery or technical assistance.
Disclaimer
The use of this news article and images came with permission from Kollmorgen.