Tue 3rd May 2022 - Why Does My Stepper Motor Get Hot?
All electric motors heat up during operation, which is simply a product of passing current through a coil of wire. Electric motors use copper wire to form coils that are part of the electromagnetic circuit required to produce rotation. While copper is a very good conductor, it does have resistance that causes the copper to heat up. The amount of current delivered to the motor along with the winding resistance determines how hot it gets. The nature of stepper motor operation requires full rated current to be applied at all times, which differs from a servo motor that provides only the required current to produce the desired motion.
Stepper motor heat sources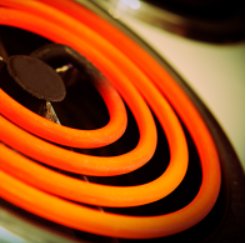
Stepper motors are designed to accommodate the heat generated when operated at their rated power. While the majority of the generated heat comes from the motor windings, there are other sources of generated heat in hybrid stepper motor designs, such as vibration and eddy currents. Since the motor is driven by a series of square wave pulses filled with various harmonic frequencies, the motor will vibrate. This vibration not only contributes to audible noise, but additional heat as well. Eddy currents are another heat producing source. The lamination steel used in the stepper motor stator can generate recirculating currents (Eddy currents) that tend to add more heat to the stator. All the heat that resides in the stepper motor stator transmits to the motor housing and endbells, which creates a motor that is definitely hot to the touch.
How to reduce stepper motor heat
While it is natural for a stepper motor to run hot, there are ways to reduce the heat. The common method is to utilize a stepper drive feature called idle current reduction that reduces the current applied to the motor to a set percentage when the motor is not moving. In many cases, the full holding torque of the stepper motor is not required during idling conditions, so the applied current can be reduced, which in turn reduces the heat generated by the motor. Other more sophisticated methods to reduce heating is to shape the current wave to minimize unwanted harmonics and to smooth out the pulses delivered to the motor, or to use a drive’s microstepping feature. Heat sinking methods can draw away heat from the motor to allow it to operate cooler as well.
It is also possible that a stepper motor and drive are mismatched, meaning that the drive’s output current is higher than the motor’s rated current. Most stepper drives can adjust the output current setting using either dip switches on the drive or within the drive software.
Kollmorgen offers
online design tools that help calculate the expected motor temperature to determine if the motor and drive are optimized to prevent over heating in the motor based on the application requirements.
About the Author
This blog was a collaborative effort among a team of motion and automation experts here at Kollmorgen, including engineers, customer service and design experts. Wherever you are in your project, we’re here to help.
=======================================================================================================================================================================
As a Gold Partner, Micromech are able to supply and provide expertise on
Kollmorgen products. Contact our sales team on
01376 333333 or
sales@micromech.co.uk for price and delivery or technical assistance.
Disclaimer
The use of this news article and images came with permission from Kollmorgen.